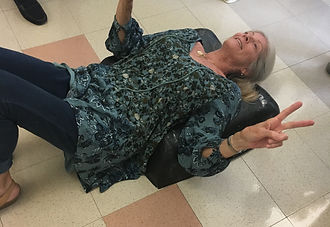
Week 10
March 15, 2017
We worked on completing the prototype in order to present the final design to Susan and the professors. We perfected the shape of the plaster mold as well as created the correct folds and attached the bottom pieces of the bed. Many hours were spent on this throughout the week. Everyone came together to make this happen.

Week 9
March 10, 2017
THE 4' x 4' PLINTH WORKS. The entire group worked for hours on end this week to complete our project. We were able to complete the one section of the plinth successfully!

Week 8
February 24, 2017
This week, our team began prepping for the Winter Design review by designing the poster. We also decided this week that we would divide the group into two, vacuum forming the original design and a new design team. We decided that we will go forth and use PVC piping as the frame work of the new design and use fabric for to hold the person up. The vacuum forming team purchased 4'x4' plastic sheets and will continue on fabricating a full size scale. Stay tuned for the life size scale coming soon!
​
New design ideas around the use of PVC pipes (which Sohee works with) are being considered. The idea of the design is based on if the pipe piece can fit in one another and resembles a scroll.
​
The 4' x 4' plinth was finally completed and installed into the vacuum former. We will be able to use it at its completion.

Week 7
February 24, 2017
This week, our team put a lot of emphasis on finishing the plinth.
​
We practiced using the vacuum former some more and finally have better understanding of how to use it We also worked to create a mold out of plaster. The process involved using the negative ABS mold and filling it with the liquid plaster and waiting for it to dry. The next day, the plaster was completely dry and completed. We touched up the mold by shaving off uneven sides and smoothing it up to resemble the final design. Next week we will be vacuum forming the plaster mold.
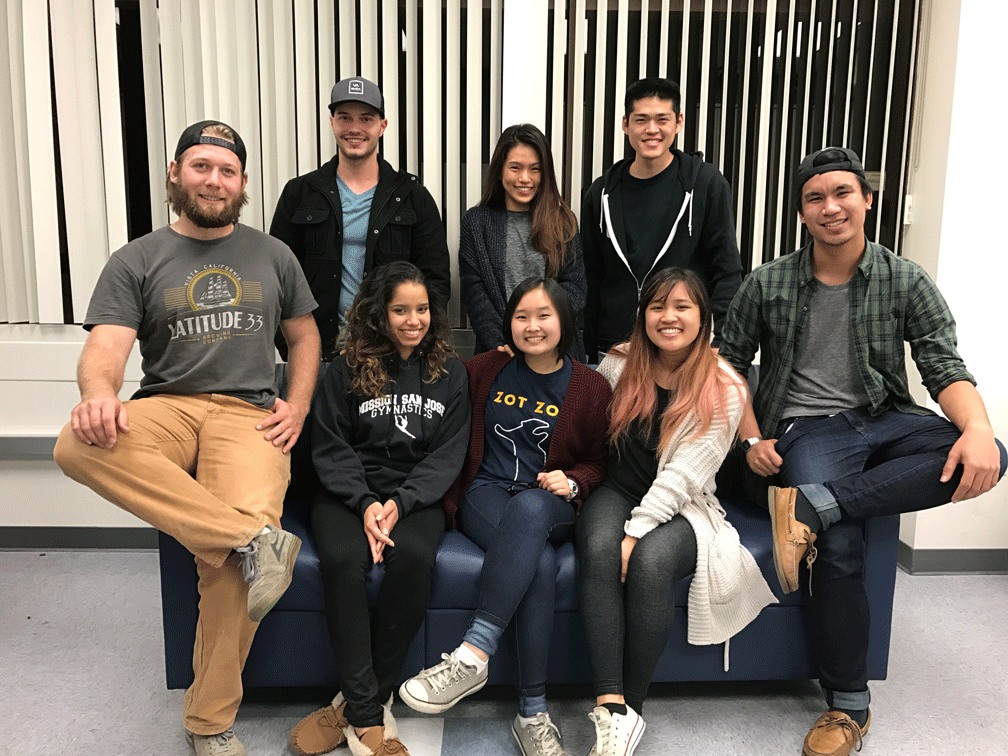
Week 6
February 17, 2017
We worked on getting our information organized for the midterm presentation.
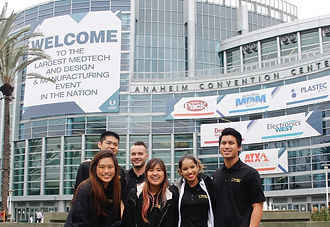
Week 5
February 10, 2017
On Tuesday, February 7, we attended the Pacific Design & Manufacturing Expo at the Anaheim Convention Center and spoke to several different manufacturing vendors in order to get a better idea of possible processes as well as quotes for the next steps after prototyping. In particular we looked for companies comfortable with producing only 50 to 100 beds at a time. These companies were quite difficult find since those numbers are considered small in the industry. Manufacturers usually work on batches of tens of thousands of items at a time. Although many companies were not interested in making our product, they gave us extremely valuable feedback on both our design and approach to manufacturing our beds.
We looked at how to create smaller scale models and decided to try modeling clay as our material of choice. The clay will be used as the object that will be pushed through the plastic on the vacuum former. We liked this material because it is easily formed and is relatively cheap for its size. The team made a trip to an arts supplies store and purchased enough clay for both the small scale and full scale models.
The Design Team tested the bed’s strength in the 3D modeling software we use. They simulated dropping the backpack to see how it would hold up under a heavy load. Unfortunately the software thought that the bed would crack if it landed on an edge. Even though the design did not meet expectations, we still learned valuable information about how the design should change in the next version.

Week 4
February 03, 2017
We continued working to get all the supplies for the plinth together this week. Updates to the design included flattening out the sides and moving locks to the side which would help to stop the bed on a track. We also reestablished the ideal weight to be 15 lbs, and nothing more.
The Fabrication Team continued to source materials needed for the plinth and began to look into alternative manufacturing processes. One of the processes discussed was silicone molding. This molding type involves pouring liquid silicone over our full scale bed until its entire surface is covered in the liquid. After a short time the silicone will harden and we will be able to remove the form. If this is done correctly, the silicone will imprint the exact shape and size of our original design. We will be able to pour a any plastic into it. Unfortunately, we were unable to use the vacuum former since the plinth was not ready and we did not have a usable scale model.
Next week we plan to attend the Pacific Design & Manufacturing Expo at the Anaheim Convention Center. Our Business Team members have been working on flyers and business cards to make sure we look professional. Also, we received our team polo shirts from the embroidery and are excited to show them off at the expo.
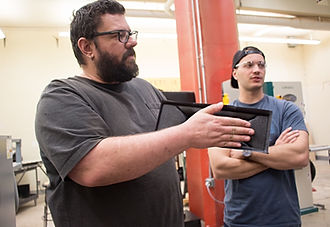
Week 3
January 27, 2017
Following up from last week, our Business Team researched and worked on a Product Proposal for the Merage New Business Venture Competition. Unfortunately, we concluded that Project Six as a consumer good would flop. The Project Proposal was red-lighted and we focused on construction of a GoFundMe page instead.
Our Fabrication Team gathered materials such as ABS and MDF to start creating the 4'x4' plinth to use as the base of the vacuum former.
​
Meanwhile, we still had access to the 2'x2' plinth, thus we practiced for the first time on the vacuum former with 2'x2', 1/8" ABS sheets. Using Derek's 3D printed model as a form for the mold, we locked the ABS in place. After the ABS melted and bellowed after a few minutes, the 3D model was then pushed upwards into the ABS and the vacuum sucked the air out to create a tight mold. As the plastic form cooled, it became difficult to take out the model since the vacuum and heat were so strong that it crushed and melted the model itself.
Cutting the mold also proved challenging once the plastic hardened. It took several minutes and heavy duty pliers. The mold in this trial had creases in the sides, thus it was unsuccessful.
​
We tried vacuum forming once again, this time adding wood blocks as reinforcement into the 3D model in order to prevent it from collapsing in again. In the end, it was still difficult to take out the form. This time we used a jig saw to cut the mold a little faster.
​
Although the trials we unsuccessful, we learned a lot. ​We will keep prototyping through next week with new methods such as clay, different plastics and thicknesses for better results.
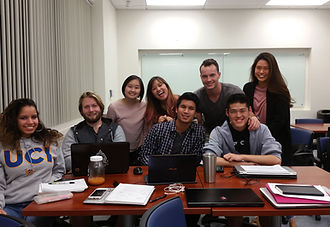
Week 2
January 20, 2017
We met our new group members, Sohee, Scott and Tim. Sohee became our new project manager this quarter. We distributed roles among the Fabrication, Design, and Business teams and discussed how to improve the current model and begin prototyping.
On Friday, the team met with Erich, who oversees the Sculpture Studio in the Arts. We received training on how to use the vacuum former. Last quarter, Jesse Jackson, Director of the Digital Arts minor, suggested contacting him about using a vacuum former to create the prototype. Erich explained how the vacuum former works step-by-step and where to find resources (plastics, mdd, etc.) online and in-store. In order to create a full-size model, we will need to construct a 4'x4' plinth. For the time being, we will create quarter-scale prototypes on the 2' x 2' plinth and familiarize ourselves with the machine.
Derek and Tim also designed new solutions for the locking mechanism and increased the thickness. Kristine started working on other possible sources of funding: the Merage Business Venture Competition and GoFundMe.
​

Week 1
January 13, 2017
The first meeting of the new year has lifted off! We regrouped and started to plan our next steps. We broke into three subgroups: Fabrication, Design, and Business team. On January 12, we met with the Prof. McDonell, Prof. Ahmadkhanlou and Susan to review prototyping methods:
​
-
Vacuum Forming (on-campus and low-cost)
-
Silicone Molding
-
Injection Molding (high-cost)
Additionally, we looked at the design and its current issues; thickness of the bed, the materials, and locking mechanism needed to be fix by the next week.